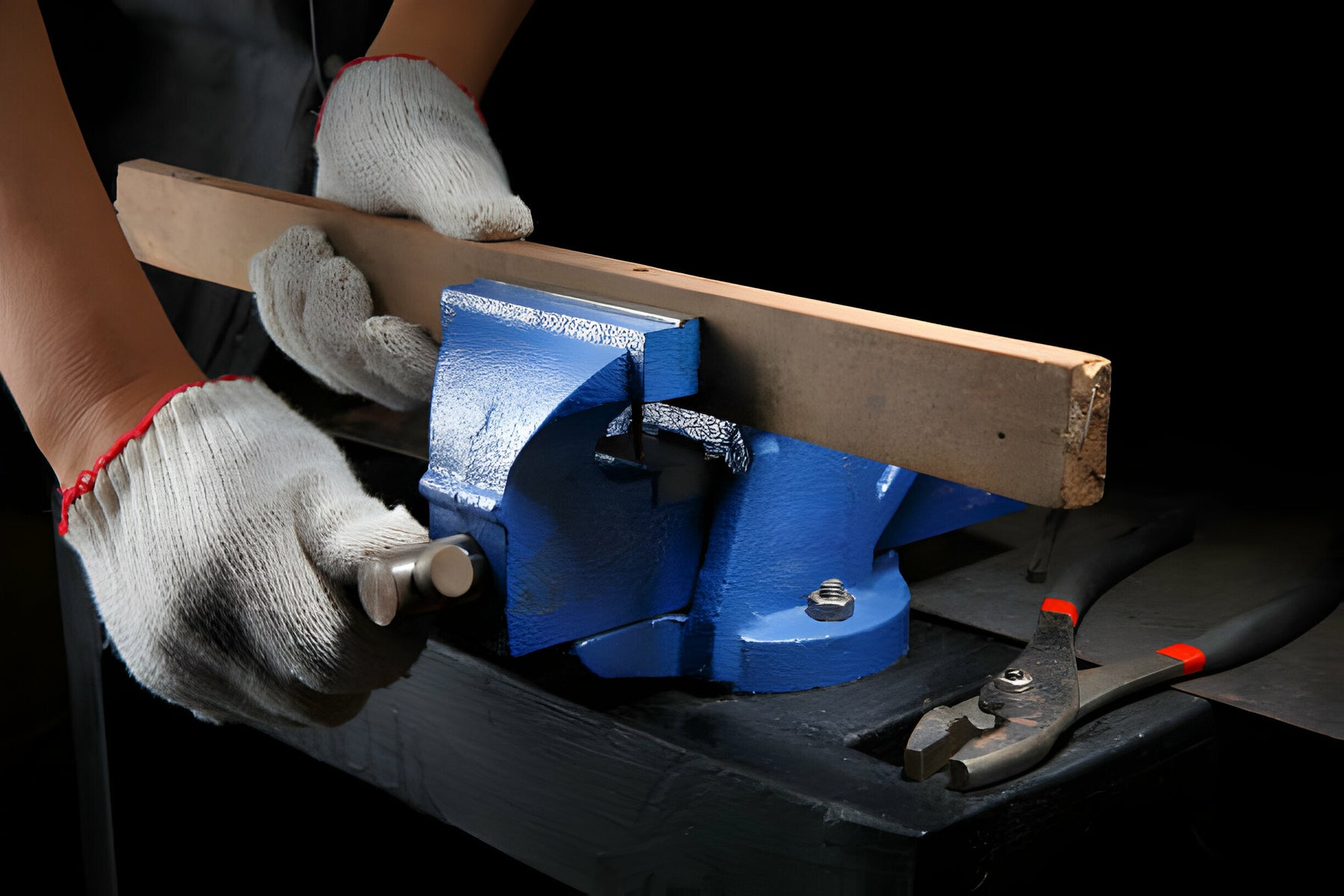
The Importance of Regular Bench Vise Lubrication
As workshop workhorses enduring constant friction, stress and environmental exposures, bench vises require diligent lubrication maintenance to achieve decades of dependable service. This comprehensive guide details best practices for 11 critical lubrication points, ensuring maximum tool lifetime through minimal efforts. Consistent lubrication is key to protecting precision mechanics from the ravages of time and conditions. With hand tools and selection of the right lubricants, vises reward meticulous owners with sustained factory performance long after expected lifespans. Understanding each component system also allows proactively catching smaller issues before deterioration necessitates expensive repairs or early replacement.
The Types and Application of Bench Vises: A Detailed Exploration
Bench vises, the cornerstone of any workshop, come in various types, each designed to cater to specific materials and applications. Understanding the diversity and application of these vises is crucial for professionals aiming to maximize their workshop's efficiency and extend the lifespan of their tools through proper maintenance, including regular lubrication. This section explores the main types of bench vises and their applications, providing insights into selecting the right vise for your projects.
1. Metalworking Vises
These are the most common type found in workshops. Metalworking vises are designed to handle the rigors of cutting, bending, and shaping metal. They typically feature hardened steel jaws for gripping metal securely without damaging it.
- Applications: Ideal for fabrication shops, machine shops, and anywhere metal is the primary material being worked on. Regular lubrication of the screw mechanism and the slide is crucial to withstand the high forces and metal shavings encountered.
2. Woodworking Vises
Woodworking vises are designed with wooden jaws or metal jaws with wood facings to prevent marring the workpiece. These vises often have a quick-release mechanism to easily adjust the opening width without turning the spindle.
- Applications: Essential in carpentry and woodworking shops for tasks like planing, chiseling, and assembly. Lubrication points include the guide bars and screw mechanism to ensure smooth operation.
3. Mechanic's Vises
Also known as engineer's vises, mechanic's vises are heavy-duty and often made from cast iron or forged steel. They have a swivel base for positioning the workpiece at different angles and serrated jaws for a firm grip.
- Applications: Suited for automotive workshops and general mechanical work. These vises experience substantial stress and require frequent lubrication of the swivel mechanism and main screw.
4. Pipe Vises
Pipe vises are specially designed for holding pipes and tubing securely during cutting or threading operations. They come in two forms: yoke and chain. Yoke vises clamp around the pipe, while chain vises use a chain to secure the pipe.
- Applications: Indispensable for plumbers and metalworkers who regularly work with pipes. Key lubrication points include the chain or yoke mechanism and the main screw.
5. Multi-Purpose Vises
These vises offer versatility with both pipe-jaw and flat-jaw capabilities, allowing them to hold a wide range of shapes and materials. They often have a rotating base to easily switch between functions.
- Applications: Great for hobbyists or workshops that handle a variety of materials and require the flexibility of different vise types in one tool. Regular lubrication of the rotation mechanism and jaws ensures smooth operation and longevity.
Understanding the types and applications of bench vises, coupled with a commitment to regular lubrication, empowers professionals to maintain their workshop tools in peak condition. This proactive approach not only enhances tool performance but also mitigates the need for costly repairs or replacements, ensuring a productive and efficient workspace.
Jaw Slides
Jaw slide surfaces experience especially high wear as they translate clamping force. Untreated steel quickly seizes or corrodes without a protective lubricating barrier. Applying a micro-thin film of premium machine oil or dry teflon lubricant to jaw tracks renews slipperiness, guarding against friction and contact damage. Periodic touch-ups restore buttery smoothness as surfaces darken. Quality lubricants also attract fewer contaminants than bargain oils prone to gunk buildup exacerbating issues down the line. Untreated, slide surfaces rapidly degrade into unusability.
Leadscrew Threads
Thread quality dictates clamping precision and longevity. While handy for loosening surface corrosion temporarily, WD-40 residuals dry out leaving threads vulnerable again. Opt instead for carefully working lightweight machine oil or anti-seize compound into the full leadscrew length and mating nut threads using a detailing brush or toothpick. Re-apply every 6-12 months or as required. Precise threading relies on consistent lubrication for dependable long-term performance.
Screw Handle Interface
The rotational interface connecting handles to leadscrew housings demands judicious lubricant selection and application. Greases too viscous attract excess dirt but dry lubricants fail protecting metal interfaces. A few selective dots of teflon-infused lithium complex grease worked thoroughly around contact edges with a lint-free cloth satisfy both needs. Barring foreign contaminant intrusion, mechanisms operate buttery-smoothly indefinitely under any torque.
Jaw Pads & Contact Points
Plastic pads buffering workpieces from direct metal contact sustain inevitable wear. Prompt replacement restores non-marring interfaces before deterioration. However, a generous coating of lightweight machine oil between new pads and their mounting surfaces drastically reduces friction with metal. Bonding pads securely while minimizing future replacement needs and material marring alike.
Rack & Pinion Head
Rack teeth and pinion gears precise enough for micro adjustments demand utmost care. Over-lubricating induces unwanted grime accumulation compromising function. Only the lightest machine or clock oil penetrating cut root areas lubricates effectively without dirtying surfaces or mechanics. Use a sewing needle or pipette to apply minimum quantities then carefully stroking gears to evenly distribute.
Swivel Base Joints
Promoting lubricated-for-life pivoting requires selecting lubricants formulated for arduous permanent immersion. Generously packing wheel bearing grade grease infused with dry graphite or molybdenum disulfide powders into mounting points saturates interfaces dependably for many rotation cycles between reapplications. Pivoting remains buttery-smooth indefinitely.
Quick-Release Mechanisms
Designed for swift clamping/unclamping, quick-release components see exhaustive use warranting diligent care. Disassembly allows thorough cleaning before generously lubing moving parts internally and externally with lightweight machine oil. Work mechanisms repeatedly to distribute lubrication into all bearing surfaces and crevices. Fluid, reliable performance persists through countless duty cycles.
Adjusting Handwheels
Periodic disassembly permits meticulous cleaning then lubricating hub/setscrew interfaces liberally with premium anti-seize compound. Graphite powder mixed sparingly into grease maintains lubricated threads without seizing. Buttery smooth precision endures indefinitely under harshest environments.
Brake/Anti-Rotation Surfaces
Subject to extreme frictional forces, braking dogs and gears demand superb lubrication preventing wear over long duty cycles. Rotate components vigorously while periodically touching up molybdenum disulfide dry film coatings to maintain non-marring, low-friction barriers excluding contaminants. Lubricated surfaces function smoothly for multiple lifetimes.
Handles & Exposed Fasteners
Applying Boeshield T-9 or equivalent wax-enhanced protectant to unpainted handles and hardware every 6-12 months fortifies steel against weathering for generations. Preventative coatings discourage corrosion and pitting from degradation without dismantling. Materials undergo endless hard use gracefully maintained like new.
Periodic Disassembly
Beyond scheduled visual inspection and touch-up lubing, committing to full annual disassembly maximizes service lives. Careful cleaning followed by cautious, meticulous reassembly with all moving components freshly lubricated restores vises to as-new condition. Digital calibrations ensure precision within factory specs. Revival rejuvenates vises to last additional lifetimes under demanding industrial usage.
Related Article: Top Tips to Avoid Common Bench Vise Mistakes
Keep Vises Tight and Gripping
In summary, periodic and diligent focus on critical lubrication points safeguards vises from inevitable wear stresses for lifetimes of invaluable service. User convenience pales compared to maximizing expensive capital equipment investments. Extending functions far beyond expected lifespans rewards minimal materials and time commitments. With lubrication stewardship, vises remain victorious workhorses utterly dominating projects indefinitely as intended from day one. Their dependability remains well-earned through proactive lubrication maintenance.